Validation
Process Validation
Ensures that a manufacturing process consistently produces products meeting quality standards. It includes Prospective, Concurrent, Retrospective, and Revalidation methods.
Confirms that cleaning procedures effectively remove residues, preventing cross-contamination between batches.
Verifies that laboratory analytical methods are accurate, reliable, and suitable for their intended use.
Cleaning Validation
Analytical Method Validation
Validation in pharmaceutical manufacturing is the documented process of ensuring that systems, equipment, and processes consistently produce results that meet predetermined quality standards. It ensures compliance with regulatory requirements (such as FDA and EMA guidelines) and guarantees product safety, efficacy, and consistency. Validation includes Installation Qualification (IQ), Operational Qualification (OQ), and Performance Qualification (PQ), ensuring that every stage of production operates within established parameters. This systematic approach minimizes risks, prevents product failures, and enhances overall manufacturing reliability.
Equipment Validation
Ensures that manufacturing equipment performs as expected. This includes Installation Qualification (IQ), Operational Qualification (OQ), and Performance Qualification (PQ).
Ensures that computerized systems used in manufacturing, quality control, and data management function correctly and comply with regulations like 21 CFR Part 11.
Ensures that analytical instruments used in QC, R&D, and stability testing operate accurately and consistently. It follows IQ, OQ, PQ to confirm installation, functionality, and performance. LEV also includes calibration, preventive maintenance, and Computer System Validation (CSV) for software-driven instruments like HPLC, GC, and spectrophotometers. Compliance with FDA 21 CFR Part 11, GLP, and USP ensures data integrity and regulatory adherence in pharmaceutical testing.
Computer System Validation (CSV)
Laboratory Equipment Validation (LEV)
Each type of validation plays a crucial role in maintaining product quality, patient safety, and regulatory compliance in pharmaceutical manufacturing.
The Pharma University
Empowering professionals in pharmaceutical manufacturing
© 2025 ThePharmaUniversity.org.
All Rights Reserved.
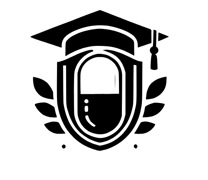
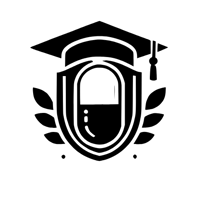